Powder coating is a modern finishing process that has transformed the way surfaces, particularly metal components, are treated. It involves applying a dry powder to a surface, which is then cured under heat to create a hard, durable finish. This technique has gained significant popularity in the automotive industry due to its numerous advantages over traditional liquid paint.
What is Powder Coating?
Powder coating is distinct from conventional paint because it uses a powdered form of paint that is electrostatically charged. This charge allows the powder to adhere effectively to the surface of the metal. After application, the coated component is heated in an oven, where the powder melts, flows, and chemically reacts to form a tough, protective layer. This process results in a smooth, uniform finish that is highly resistant to wear and corrosion.
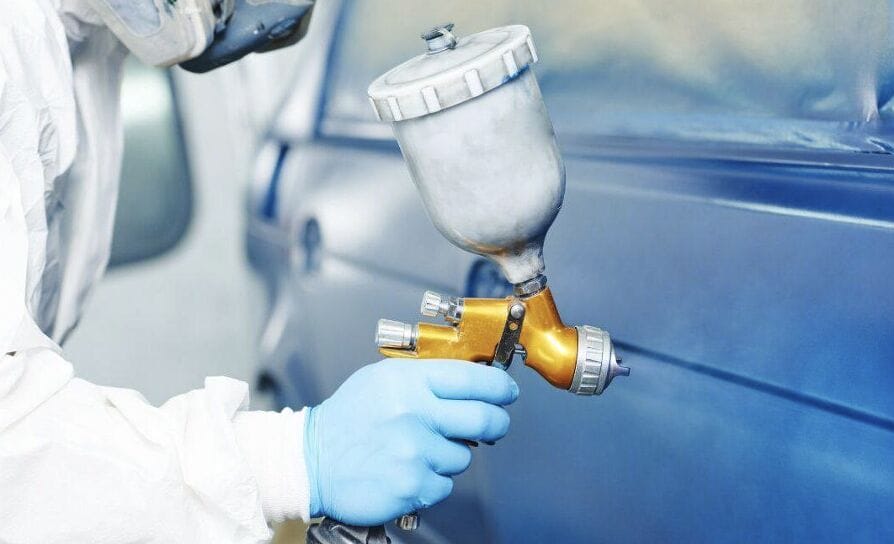
The Basics of the Powder Coating Process
1. Surface Preparation: Proper preparation is essential. The surface must be cleaned to remove any contaminants, such as dirt, oil, or rust. This step often involves methods like sandblasting or chemical cleaning to ensure optimal adhesion.
2. Application of Powder: Using an electrostatic spray gun, the powder is evenly applied to the grounded metal surface. The charged particles cling to the surface, ensuring even coverage.
3. Curing: The coated component is then placed in an oven, typically heated to temperatures between 350°F and 400°F (about 177°C to 204°C). This curing process allows the powder to melt and adhere to the substrate, creating a hard finish.
4. Cooling and Inspection: Once cured, the component is allowed to cool, after which it undergoes rigorous inspection to ensure it meets quality standards.
Why Choose Powder Coating in the Automotive Industry?
The automotive industry requires materials that can withstand extreme conditions, and powder coating offers several advantages:
1. Exceptional Durability
One of the primary reasons for using powder coating is its durability. It is significantly tougher than conventional paint and can resist scratches, chipping, fading, and wearing. This is particularly important for automotive components, which are exposed to a wide range of environmental conditions.
2. Superior Corrosion Resistance
Vehicles are susceptible to rust and corrosion, particularly in areas where moisture can accumulate. Powder coating provides an effective barrier against these elements, helping to extend the lifespan of automotive parts.
3. Environmental Benefits
Powder coating is more environmentally friendly than traditional paint. It contains no solvents, which means it emits negligible volatile organic compounds (VOCs) during application. This makes it a safer choice for manufacturers looking to reduce their environmental footprint.
4. Aesthetic Flexibility
Powder coating is available in an extensive array of colors and finishes. This flexibility allows automotive manufacturers to create unique looks and styles that appeal to consumers. Options include matte, glossy, and textured finishes, providing endless customization possibilities.
5. Cost-Effectiveness
While the initial investment in powder coating may be higher than traditional painting methods, the long-term savings can be significant. The durability of powder-coated finishes means that maintenance and repair costs are reduced, making it a wise investment for automotive manufacturers.
Key Applications of Powder Coating in the Automotive Industry
1. Automotive Wheels
Powder coating is extensively used on automotive wheels. The process provides a protective layer that guards against scratches, chips, and corrosion. With a variety of color and finish options, powder-coated wheels enhance the overall aesthetic appeal of vehicles.
2. Chassis and Frames
The chassis and frames of vehicles require strong protection against environmental damage. Powder coating creates a robust barrier that prevents rust and deterioration, ensuring that these critical components remain functional over time.
3. Engine Components
Engine parts are subjected to extreme temperatures and harsh conditions. Powder coating offers heat resistance and protects against corrosion, making it ideal for components such as brackets, covers, and housings.
4. Body Panels
Powder coating can also be applied to various body panels of vehicles. This not only improves the visual appeal but also provides protection from UV rays, moisture, and dirt, helping to maintain the vehicle’s appearance over time.
5. Interior Components
In addition to exterior applications, powder coating is used for interior parts like dashboard frames, door handles, and trim. This ensures that interior components are durable and maintain their aesthetic appeal.
Quality Control in Powder Coating
Quality control is a crucial aspect of the powder coating process. Ensuring that the final product meets specific standards involves several steps:
1. Pre-Coating Inspection
Before powder coating, parts are inspected for surface defects and contamination. Any imperfections must be addressed to ensure proper adhesion of the powder.
2. Thickness Measurement
After coating, the thickness of the powder layer is measured to ensure it meets specified requirements. This can be done using various instruments to gauge the coat’s uniformity.
3. Adhesion Testing
Adhesion tests are performed to ensure that the powder coating bonds effectively to the substrate. This is critical for ensuring the durability of the finish.
4. Visual Inspection
Final visual inspections are conducted to check for any defects, such as uneven coverage, bubbles, or discoloration. Any parts that do not meet quality standards are reworked or discarded.
Choosing the Right Powder Coating Partner: Proto MFG
When selecting a powder coating provider, it’s essential to choose a company that specializes in automotive applications. Proto MFG prides itself on its expertise in the powder coating process, ensuring that clients receive the highest quality service. Here are some reasons to choose Proto MFG:
1. Expertise and Experience
With years of experience in the industry, Proto MFG has developed a deep understanding of the unique requirements of automotive powder coating. Their team is skilled in delivering consistent and high-quality results.
2. Advanced Technology
They utilize the latest technology and equipment in their powder coating processes. This ensures precision in application and curing, leading to superior finishes that meet the demands of the automotive sector.
3. Customization Options
At Proto MFG, they understand that every manufacturer has specific needs. They offer a wide range of colors and finishes to meet the unique aesthetic and functional requirements of our clients.
4. Commitment to Quality
Quality is at the forefront of everything they do. Their rigorous quality control measures ensure that every product that leaves their facility meets the highest standards of durability and appearance.
5. Environmental Responsibility
Proto MFG is committed to environmentally responsible practices. Their powder coating processes are designed to minimize waste and reduce emissions, aligning with the growing demand for sustainable manufacturing solutions.
The Future of Powder Coating in the Automotive Industry

As the automotive industry continues to evolve, so too does the demand for advanced finishing solutions like powder coating. Some trends that are shaping the future of this technology include:
1. Technological Advancements
Innovations in powder coating technology are expected to enhance application efficiency and finish quality. New formulations are being developed to improve performance characteristics, such as resistance to heat, chemicals, and UV radiation.
2. Sustainability Initiatives
With increasing focus on sustainability, the automotive industry is seeking eco-friendly solutions. Powder coating fits this need perfectly, and manufacturers will likely continue to invest in sustainable practices, including energy-efficient curing methods.
3. Increased Customization
As consumers increasingly seek personalized vehicles, the demand for customized finishes will grow. Manufacturers will turn to companies like Proto MFG that can offer a wide range of customization options to meet these preferences.
4. Expanded Applications
The applications of powder coating are likely to expand beyond traditional automotive parts. New materials and substrates are being explored, allowing for innovative uses in various automotive applications.
Challenges in Powder Coating
While powder coating offers numerous advantages, there are also challenges to consider:
1. Initial Setup Costs
The setup costs for powder coating facilities can be higher than those for traditional painting systems. However, this is often offset by long-term savings due to reduced maintenance and longer lifespan of the coatings.
2. Limited Flexibility for Small Batches
Powder coating can be less flexible for smaller production runs. The process is most efficient at larger scales, which may not suit all manufacturers. However, companies like Proto MFG are equipped to handle both large and small orders effectively.
3. Color Matching
While powder coating offers a wide variety of colors, achieving precise color matching can sometimes be a challenge. This requires careful planning and testing to ensure consistency across different batches.
Conclusion
Powder coating has established itself as a critical process in the automotive industry, offering unparalleled durability, aesthetic appeal, and environmental benefits. From automotive wheels to interior components, the application of powder coating enhances both the performance and appearance of vehicles. Companies like Proto MFG are leading the charge in providing high-quality powder coating solutions tailored to the unique needs of the automotive sector.
As the industry continues to evolve, the importance of powder coating will only grow. Its ability to withstand harsh conditions, coupled with the flexibility for customization, positions it as a vital component in modern automotive manufacturing. For automotive manufacturers looking to enhance their products, investing in powder coating is a decision that promises long-term rewards.